VT-90H CCL/Laminate VT-90H PP/Prepreg
UL Approval: E214381 Version: 21/02/2020 /40/41/42/43Storage Condition & Shelf Life
Prepreg | Laminate | |||
---|---|---|---|---|
Storage Condition | Temperature | < 23℃ (73℉) | < 5℃ (41℉) | Room |
Relative Humidity | < 55% | / | / | |
Shelf Life | 3 Months | 6 Months | 24 Months |
Prepreg exceeding shelf life should be retested.
Precautions In Handling
- The prepreg exceeding shelf time should be retested.
- Take care in handling thin core laminates as they are easily damaged.
- If the prepreg is not consumed within 48hrs after opening the vacuum package, it is recommended that the bags be resealed.
- Material is available in both long and short grain. The grain direction is indicated on the label with an arrow.
Designing And Inner Layer Process
- Please be careful when single ply of 1080, 1086, 1078 or 106 prepreg is designed to the dielectric layer.
- Dimension stability is the same as Standard FR4 material.
- Please check with your oxide vendor to make sure that our material is suitable with your oxide process. We recommend to control the peel strength with brown oxide copper over 2 Lb/in.
- For unclad or single sided laminates to be used in multilayer, please brush unclad sides before use.
Prepreg Availability
E-Glass styles: 7628, 1506, 1500, 2113, 2313, 3313, 2116, 1080, 1086, 1078, 106, 1067 etc.Prepreg Availability
PP Type | Resin Content | Press Thickness (mil) | DK | DF | Remark | ||||||
---|---|---|---|---|---|---|---|---|---|---|---|
@ 1GHz | @ 2GHz | @ 5GHz | @ 10GHz | @ 1GHz | @ 2GHz | @ 5GHz | @ 10GHz | ||||
7628 | 44% | 8.00 | 4.30 | 4.25 | 4.25 | 4.20 | 0.011 | 0.011 | 0.012 | 0.012 | Standard |
7628 | 40% | 7.30 | 4.40 | 4.35 | 4.35 | 4.30 | 0.010 | 0.010 | 0.011 | 0.011 | Standard |
1506 | 46% | 6.80 | 4.25 | 4.20 | 4.20 | 4.15 | 0.011 | 0.011 | 0.012 | 0.012 | Standard |
2116 | 56% | 5.40 | 3.98 | 3.93 | 3.93 | 3.88 | 0.012 | 0.012 | 0.013 | 0.013 | Standard |
2116 | 53% | 5.10 | 4.10 | 4.05 | 4.02 | 3.97 | 0.011 | 0.011 | 0.012 | 0.012 | Standard |
2116 | 50% | 4.70 | 4.15 | 4.10 | 4.10 | 4.05 | 0.011 | 0.011 | 0.012 | 0.012 | Standard |
2113 | 57% | 4.30 | 3.98 | 3.93 | 3.93 | 3.88 | 0.012 | 0.012 | 0.013 | 0.013 | Standard |
1080 | 63% | 3.10 | 3.72 | 3.67 | 3.67 | 3.62 | 0.012 | 0.012 | 0.013 | 0.013 | Standard |
1080 | 60% | 2.80 | 3.80 | 3.75 | 3.75 | 3.70 | 0.012 | 0.012 | 0.013 | 0.013 | Standard |
106 | 70% | 2.00 | 3.55 | 3.50 | 3.50 | 3.45 | 0.013 | 0.013 | 0.014 | 0.014 | Standard |
① Press thickness test condition---Prepreg lamination size 18”*24”, Copper Foil---1oz/1oz, Flow---about 5%; ② Make laminated prepreg to micro-section and measure the thickness with microscope; this thickness is used for resistance design calculation. ③ The thickness measured with micrometer is 0.2~0.4 mil larger than that measured with micro-section; and mainly used for total thickness design calculation.
Laminate Availablity
Thickness: 0.002” (0.05mm) to 0.200” (5mm), available in sheet or panel form Copper Foil: 1/4 to 12oz, HTE or RTF or DST DK values are for impedance design.Core thk. (Inches) | Stack-up | Resin Content | DK | DF | Remark | ||||||
---|---|---|---|---|---|---|---|---|---|---|---|
@ 1GHz | @ 2GHz | @ 5GHz | @ 10GHz | @ 1GHz | @ 2GHz | @ 5GHz | @ 10GHz | ||||
0.002 | 1-106 | 70% | 3.55 | 3.50 | 3.50 | 3.45 | 0.013 | 0.013 | 0.014 | 0.014 | Standard |
0.003 | 1-1080 | 63% | 3.72 | 3.67 | 3.67 | 3.62 | 0.012 | 0.012 | 0.013 | 0.013 | Standard |
0.0035 | 1-2113 | 49% | 4.12 | 4.07 | 4.07 | 4.02 | 0.011 | 0.011 | 0.012 | 0.012 | Standard |
0.0035 | 2-1067 | 58% | 3.98 | 3.93 | 3.93 | 3.88 | 0.012 | 0.012 | 0.013 | 0.013 | 2ply |
0.004 | 1-2116 | 44% | 4.30 | 4.25 | 4.25 | 4.20 | 0.011 | 0.011 | 0.012 | 0.012 | Standard |
0.004 | 2-1078 | 45% | 4.30 | 4.25 | 4.25 | 4.20 | 0.011 | 0.011 | 0.012 | 0.012 | 2ply |
0.005 | 1-2116 | 53% | 4.10 | 4.05 | 4.02 | 3.97 | 0.012 | 0.012 | 0.013 | 0.013 | Standard |
0.005 | 2-1078 | 54% | 4.10 | 4.05 | 4.02 | 3.97 | 0.012 | 0.012 | 0.013 | 0.013 | 2ply |
0.006 | 1-1506 | 42% | 4.35 | 4.30 | 4.30 | 4.25 | 0.010 | 0.010 | 0.011 | 0.011 | Standard |
0.006 | 2-1080 | 63% | 3.72 | 3.67 | 3.67 | 3.62 | 0.012 | 0.012 | 0.013 | 0.013 | 2ply |
0.007 | 1-7628 | 40% | 4.40 | 4.35 | 4.35 | 4.30 | 0.010 | 0.010 | 0.011 | 0.011 | Standard |
0.007 | 2-2113 | 48% | 4.22 | 4.17 | 4.17 | 4.12 | 0.011 | 0.011 | 0.012 | 0.012 | 2ply |
0.008 | 1-7628 | 44% | 4.30 | 4.25 | 4.25 | 4.20 | 0.011 | 0.011 | 0.012 | 0.012 | Standard |
0.008 | 2-2116 | 44% | 4.30 | 4.25 | 4.25 | 4.20 | 0.011 | 0.011 | 0.012 | 0.012 | 2ply |
0.010 | 2-2116 | 53% | 4.10 | 4.05 | 4.02 | 3.97 | 0.011 | 0.011 | 0.012 | 0.012 | Standard |
0.012 | 2-1506 | 42% | 4.35 | 4.30 | 4.30 | 4.25 | 0.010 | 0.010 | 0.011 | 0.011 | Standard |
0.014 | 2-7628 | 40% | 4.40 | 4.35 | 4.35 | 4.30 | 0.010 | 0.010 | 0.011 | 0.011 | Standard |
0.014 | 3-2116 | 53% | 4.10 | 4.05 | 4.02 | 3.97 | 0.011 | 0.011 | 0.012 | 0.012 | Non-7628 |
0.016 | 2-7628 | 44% | 4.30 | 4.25 | 4.25 | 4.20 | 0.011 | 0.011 | 0.012 | 0.012 | Standard |
0.018 | 2-7628+1-2116 | 40% | 4.40 | 4.35 | 4.35 | 4.30 | 0.010 | 0.010 | 0.011 | 0.011 | Standard |
0.020 | 2-7628+1-2116 | 41% | 4.40 | 4.35 | 4.35 | 4.30 | 0.010 | 0.010 | 0.011 | 0.011 | Standard |
0.024 | 3-7628 | 44% | 4.30 | 4.25 | 4.25 | 4.20 | 0.011 | 0.011 | 0.012 | 0.012 | Standard |
0.028 | 4-7628 | 40% | 4.40 | 4.35 | 4.35 | 4.30 | 0.010 | 0.010 | 0.011 | 0.011 | Standard |
0.029 | 4-7628 | 41% | 4.40 | 4.35 | 4.35 | 4.30 | 0.010 | 0.010 | 0.011 | 0.011 | Standard |
0.031 | 4-7628 | 43% | 4.33 | 4.28 | 4.28 | 4.23 | 0.010 | 0.010 | 0.011 | 0.011 | Standard |
0.036 | 5-7628 | 40% | 4.40 | 4.35 | 4.35 | 4.30 | 0.010 | 0.010 | 0.011 | 0.011 | Standard |
0.039 | 5-7628 | 43% | 4.33 | 4.28 | 4.28 | 4.23 | 0.010 | 0.010 | 0.011 | 0.011 | Standard |
0.042 | 6-7628 | 40% | 4.40 | 4.35 | 4.35 | 4.30 | 0.010 | 0.010 | 0.011 | 0.011 | Standard |
0.045 | 6-7628 | 41% | 4.38 | 4.33 | 4.33 | 4.28 | 0.010 | 0.010 | 0.011 | 0.011 | Standard |
0.049 | 7-7628 | 40% | 4.40 | 4.35 | 4.35 | 4.30 | 0.010 | 0.010 | 0.011 | 0.011 | Standard |
0.059 | 8-7628 | 42% | 4.35 | 4.30 | 4.30 | 4.25 | 0.010 | 0.010 | 0.011 | 0.011 | Standard |
Press Condition
1. Heating rate(Rise of Rate) of material [Material Temperature]
Programmable Press: 1.5-3.0℃/min (3~5℉/min). Manual Press:3~6℃ /min (5~10℉/min)
2. Curing Temperature & Time:
1)120~150min at more than 218℃(424℉) [Material Temperature] depending on total thickness. Boards thicker than 3 mm may need longer curing time.
2)For sequential lamination use 120 minutes for the first lamination and 150 minutes for the final. After pressing, Tg should be performed for further verification.
3. Full Pressure : ≥400psi
4. Vacuuming should be continued until over 200℃ (392℉) [Material Temperature]
5. Cold Press condition:
Keep Plate @ Room Temperature by water, Pressure:100psi, Keep Time:60minutes
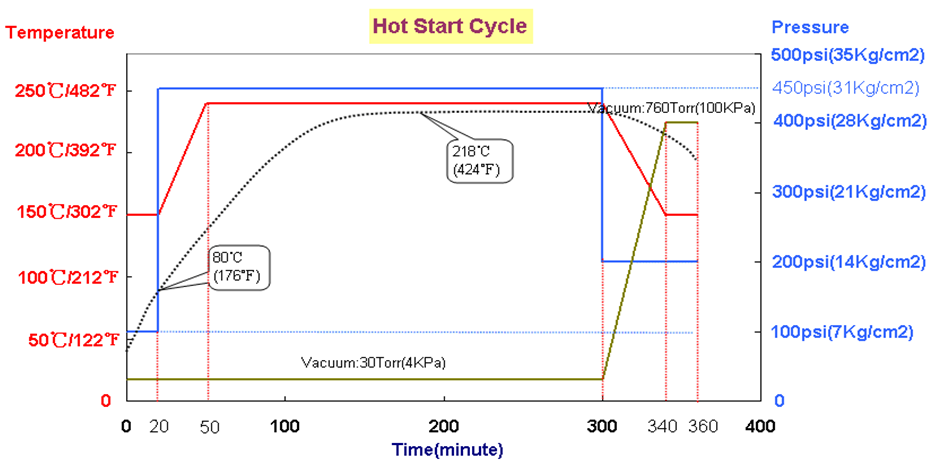