03 三月 2015
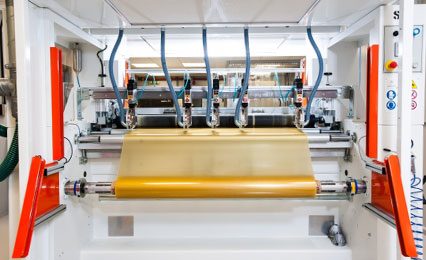
Squeeky-clean! Ventec Europe continues investment in FOD elimination.
Back in July, I took the opportunity to check out recent developments at Ventec Europe's UK Distribution Centre. It was clear that continuing investment was being committed to the establishment and maintenance of meticulous cleanliness in the pre-preg handling areas and Mark Goodwin, Ventecs chief operating officer for Europe and the US, explained the strategy: You are aware that we have always made every effort to ensure that the pre-preg we deliver is completely free from foreign object debris in the form of particulate contamination. Ventec Electronics have put enormous investment into establishing and managing a critically clean manufacturing process for prepregs and laminates, and monitoring production with advanced inspection technology. We are determined to maintain those cleanliness standards all the way into the customers lay-up room and our fabrication equipment and environment here in Ventec Europe have been specifically designed to aerospace standards. As you know, the European Space agency sees contamination of laminates by foreign material in the dielectric as a major problem, and is collaborating with key suppliers to mitigate the risk and seeking support from laminate manufacturers to define a new procurement specification in the form of Appendix A to IPC-4101-DÂÂ.
Here we are in December, with Goodwin proudly revealing the latest outcome of his continuous improvement programme: two immaculately presented clean rooms, one each for poyimide and epoxy pre-preg cutting and packing. You can look through the windows, but only trained operators in full clean-room outfits are allowed in there! See above the Pasquato slitter-sheeters we have now installed certified ISO Class 7 canopies, so that each machine has a constant laminar down-flow of highly filtered air to give an ultra-clean operating environment with real-time monitoring of temperature and humidity.
Goodwin explained the principles of operation: We only work in full rolls of prepreg; once a roll is transferred from the cold store to a slitting machine, we slit the whole roll so that there is no backwards-and-forwards traffic of part-rolls. When a roll is loaded onto a machine, the outer layer of prepreg is threaded through and discarded. Then we proceed to cut panels until the end-of roll detector stops the machine and we discard the tail-end of the roll to avoid adhesive transfer. Cut panels are removed from the machine in stacks and the top panel of each stack is inspected before packing. The pre-preg leaves the clean environment in sealed aluminised packs. Our labelling system is fully barcode- and human-readable, with full product-identity, lot-number, quantity and customer-reference details.
No card or wood is permitted in the pre-preg processing rooms, and you will notice that all the work-surfaces are stainless steel and that each room has its own set of dedicated handling equipment, colour coded to identify where it belongs and never leaving that area, to eliminate the risk of cross-contamination.. Outside in the warehouse area we are actively working towards excluding dust, and are about to fit wheel cleaners at the entrance from the loading bay to prevent fork trucks carrying dust in from outside.
In September this year we publicly declared our commitment to support the proposal led by the European Space Agency to define an enhanced quality standard for base materials used in high-reliability PCBs for critical applications, with particular reference to the prevention and detection of foreign material inclusions early in the supply chain. Even though Appendix A to IPC-4101-D has yet to be formally adopted, we already have customers calling-up ESA requirements on their purchase orders. And if we use ESA as our default standard, then our whole customer base benefits as a result.
Pete Starkey, I-Connect007, December 2014